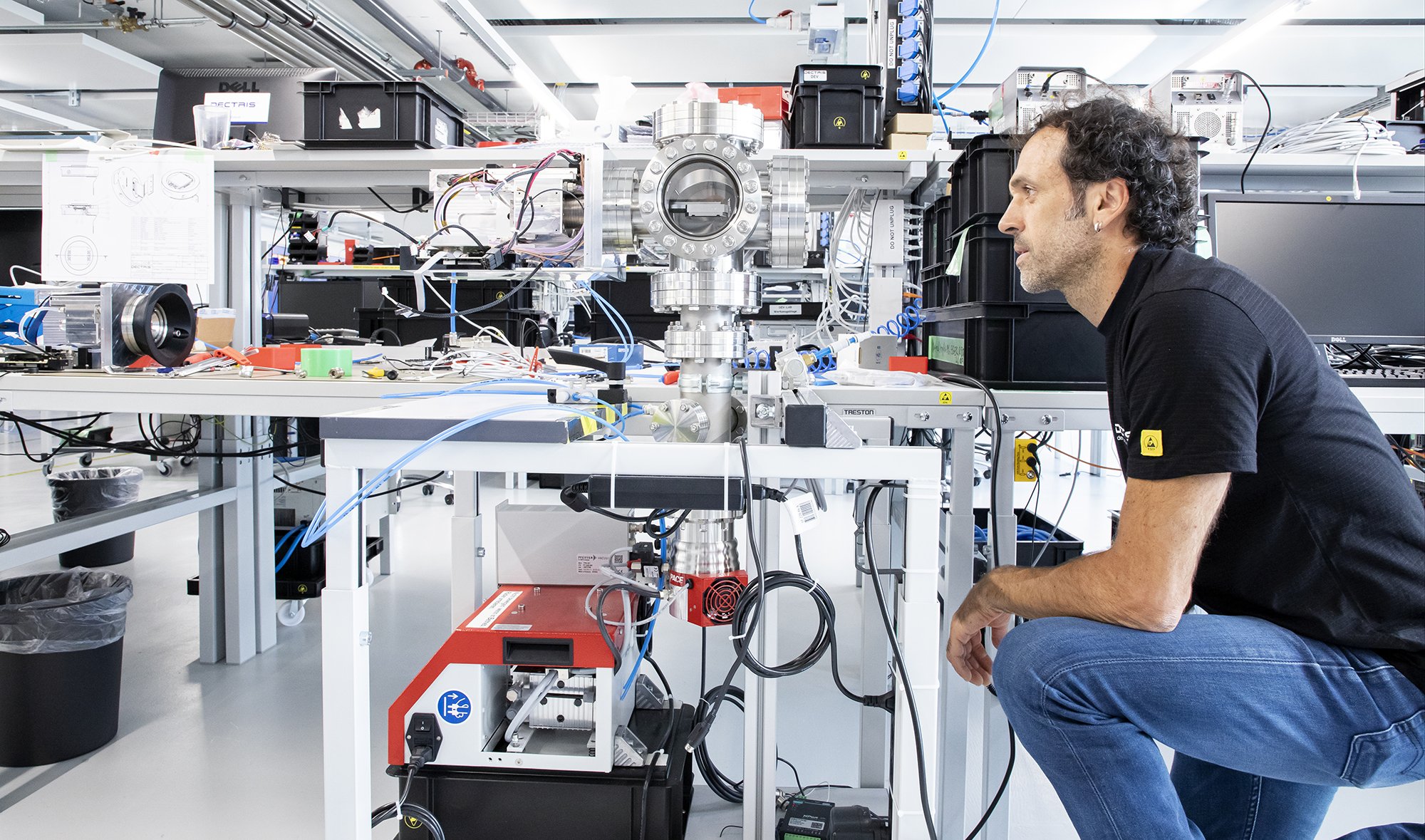
Dr. Christoph Hörmann at the DECTRIS development lab working on DECTRIS QUADRO.
Dr. Christoph Hörmann at the DECTRIS development lab working on DECTRIS QUADRO.
A 15-minute read
When bringing a high-tech product to the scientific community, delivering a detector that answers all the performance requirements is the first (and probably most straightforward) step. However, what does it mean to commercialize a technology? We asked Dr. Christoph Hörmann, Project Manager Development at DECTRIS, and our employee 007, to tell us about his experience with developing X-ray and electron detectors.
Detectors have accompanied Christoph from Day One of his career. He did his diploma thesis at the Paul Scherrer Institute (PSI) in the Swiss Light Source (SLS) detector group that was led by Dr. Christian Brönnimann, the future founder of DECTRIS. Supervised by Dr. Bernd Schmitt, Christian Brönnimann’s successor as the head of the SLS detector group, Christoph worked on the development and characterization of the first-generation MYTHEN detector modules for the SLS Materials Science beamline. Then, for his Ph.D. under the supervision of Dr. Roland Horisberger, he joined the High-Energy Physics Group of the PSI. The group was responsible for developing the Compact Muon Solenoid (CMS) barrel pixel detector for the Large Hadron Collider (LHC) at CERN. Fun fact: today, at DECTRIS, Christoph and Roland are again working side by side! After obtaining his Ph.D., Christoph joined Sensirion AG as a Project Manager for humidity sensors. There, he gathered a lot of experience with commercializing high-tech products. However, still fascinated by technology and science, he never lost touch with his detector family. When the opportunity to “go back to his roots” presented itself in 2008, he applied for the position of Detector Physicist at DECTRIS and joined the company as employee number seven.
DECTRIS: What led you to DECTRIS?
Dr. Christoph Hörmann, Project Manager Development at DECTRIS: It felt like a homecoming. I enjoyed my experience in the high-tech industry and learned a lot about what it meant to develop a commercial product for an industrial partner: assuring reproducibility through process development and standardization, delivering economically viable solutions, obtaining necessary certifications, building customer support, increasing user-friendliness, maintaining documentation, and so on. However, oftentimes, commercial development - as I experienced it - had little to do with delivering maximum performance.
I missed that scientific eagerness to get the most out of a technology and push its limits. I missed the scientific community. At DECTRIS, I felt I could find the right balance between scientific and commercial development. Not to mention that the project I was hired for was the commercialization of the MYTHEN detector, which I knew like the back of my hand.
DECTRIS: What is your role in the company today?
Christoph: My role has transformed a lot over the years. I started as a detector developer and spent most of my time in the laboratory: improving calibration routines, drawing Printed Circuit Boards (PCBs), or working on mechanical designs. However, by the time the MYTHEN and MYTHEN2 detector product families were successfully transferred to production, the situation at DECTRIS had changed. The company grew: we had more developers, but also more numerous and complex projects. That is when my role started to shift toward project management. One of my first projects was the development of the EIGER2 R 500K X-ray detector for laboratory applications.
Today, however, I am responsible for all the development projects for electron microscopy detectors. As a Project Manager, I contribute to the ideation of a new product and project proposal; take care of the system concept, feasibility study, and risk management; and estimate the effort and approximate schedule. I accompany the project until the delivery release and the ensuing industrialization phase.
This entire process is quite creative and exciting. It is always a thrill to deliver the first feasibility model - or a prototype - to customers and receive their feedback, to see the product launched, and to learn about the many creative ways the scientists use it to reach their goals.
DECTRIS: During your first years at DECTRIS, you have been working on X-ray detectors (MYTHEN and EIGER). What did you learn from this experience that you can apply to the development of electron detectors?
Christoph: The experience and knowledge I acquired in my career are twofold. On the one hand, throughout my studies and work with X-ray detectors, I gained a deeper understanding of hybrid-pixel technology that is used in DECTRIS cameras. Since our X-ray and electron detectors are based on the same technological concepts, the company’s and my background in X-ray detection accelerated the development process of our electron microscopy portfolio. On the other hand, I also learned (sometimes the hard way) what it means to bring technology to the market. Designing a detector that would answer all of a user’s requirements is just one part of the puzzle. Delivering an easy-to-use, reliable, and certified product to a customer or Original Equipment Manufacturer (OEM), and building support and commissioning services, is a different story.
DECTRIS has 15 years of experience with commercializing the detector technology, and this helps us a lot, to avoid some pitfalls on our way. That being said, we did have to learn a lot about electron microscopy and its applications to best adapt our hybrid-pixel technology to electron detection.
DECTRIS: What were your biggest challenges in the development of electron detectors?
Christoph: To begin with, we needed to establish a common language with electron microscopists. At first, we were investigating mostly Life Science applications. Back then, most of the scientists we talked to used integrating detectors and were unfamiliar with our technical specification jargon, such as “count rate”, “frame rate”, “threshold”, and so on. We had to understand the applications in combination with all the parameters and learn to convert them accordingly, to be able to explain the performance of our detector or understand the communities’ needs. This required a deeper knowledge of electron microscopy techniques, which we also lacked. Finding out the requirements for vacuum compatibility, vacuum feedthroughs, mechanical movements, X-ray shielding, and ASIC performance was challenging, as they differ significantly from what we were used to in the X-ray community.
Very quickly, we bridged the gap in our knowledge by bringing experienced microscopists on board and kicking off collaborations with several laboratories across Europe. It is thanks to users’ feedback that we were able to adjust our development on the go and move from adapting existing technology for electron detection to developing a dedicated ASIC, specific calibration, retractable mechanisms, and high vacuum compatibility.
DECTRIS: Can you share with us your low and high moments on the job?
Christoph: As a Project Manager, I remember some harsh feedback from our OEM partners with regard to one of our X-ray detectors. We were told that the EIGER2 R 500K “will never become a product” based on its performance. The problem was a bug in the ASIC that appeared under some extreme conditions. It caused some delays in our joint venture; nevertheless, this collaboration turned out to be successful.
As for the highlights, I am not impartial to the success of the MYTHEN detector family - by far, our most-sold X-ray detector. Also, the characterization of the DECTRIS ELA EELS detector by Nion was a motivating factor for the whole team. One of the most recent highlights was, of course, the launch of the ARINA 4D STEM detector last summer (2022) and the work we have done with several laboratories during the prototyping phase of development. The feedback we got from the community, and the results scientists were able to obtain with this detector, are very encouraging. There could not have been a better reward for me and the team! A moment worth popping a bottle of champagne!
DECTRIS at M&M 2022 after the launch of the ARINA detector. FLTR: Matthias Meffert, Daniel Stroppa, Christoph Hörmann, Luca Piazza, Vittorio Boccone, Darya Bachevskaya, Clemens Schulze-Briese.
DECTRIS: What do you imagine for the next electron detector by DECTRIS?
Christoph: I, personally, would be interested in developing dedicated readout data acquisition electronics to have the detector control unit (DCU) embedded in the system. This would require new software as well. But we have many ideas that we would like to proceed with, so let’s see where we will be in a couple of years.
DECTRIS: You were employee number seven at DECTRIS. Can you tell us how the company changed over the years?
Christoph: At the very beginning, things were quite simple. We were a group of detector physicists working together on everything. It was easy to make a decision over a lunch or coffee break.
As the company grew, a lot of processes and regulations started to appear. It was necessary, but at times a bit restrictive. Naturally, the organization and structures have developed around X-ray detector development and commercialization, as this was the company’s main focus.
When DECTRIS decided to adapt its technology for electron detection, some of us who were involved in the development of the new products went back to the old times to gain more flexibility and agility in our work. As more of us at DECTRIS join the electron microscopy projects, a new set of processes is being defined to mainstream our efforts.